Inventory Accounting for Ecommerce: Step-by-Step Guide
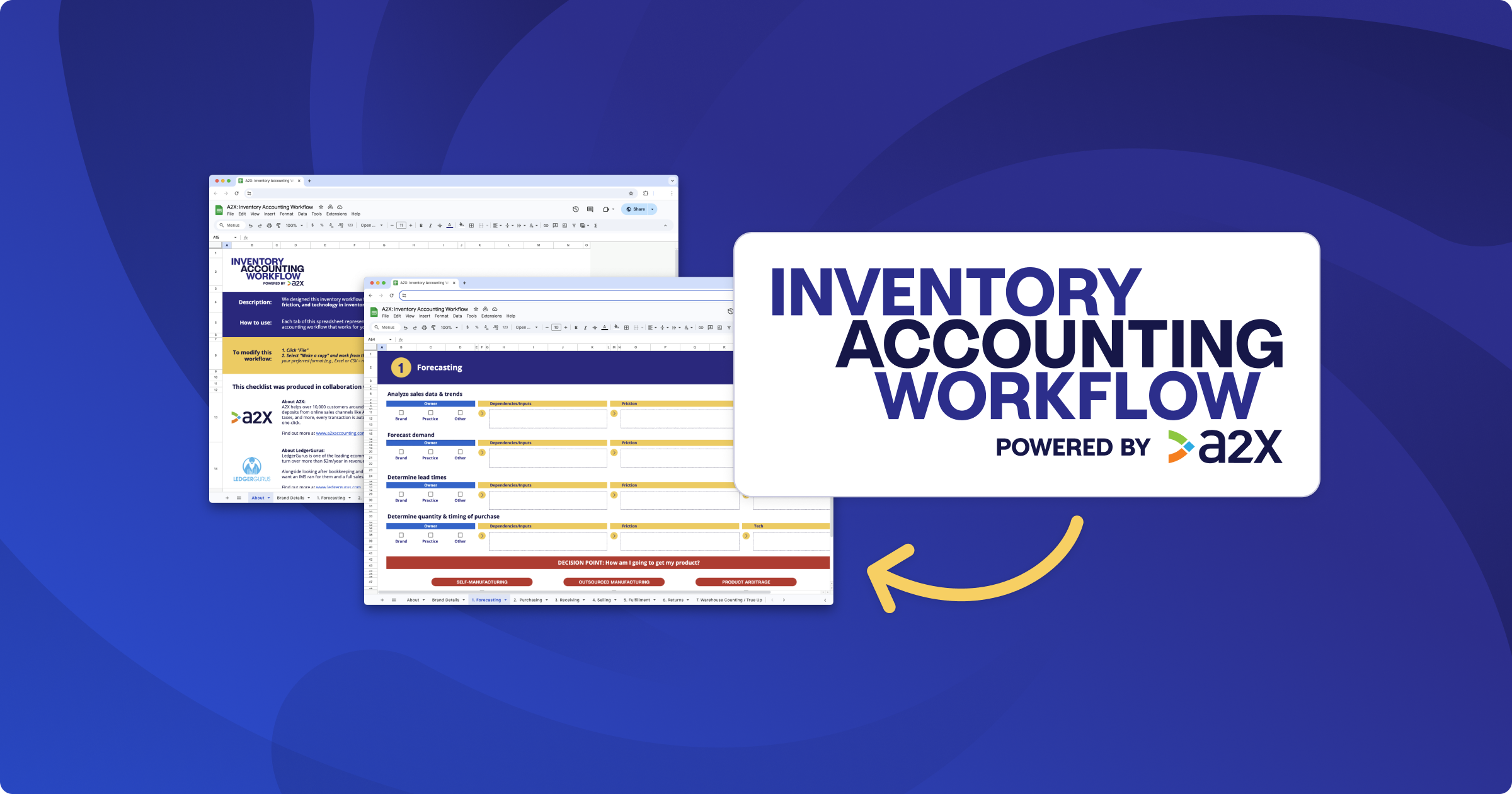
Ask any online seller (or accounting professional supporting one) about inventory accounting, and they’ll tell you that it’s a huge challenge. The multitude of moving parts can make the most experienced sellers dizzy.
That’s why it’s important to have an overview of the entire inventory accounting process so that you can identify where information might be falling through the cracks or where inefficiencies are causing friction.
In this guide, we’ll provide an overview of each step in the inventory accounting process. These inventory accounting steps were provided by inventory accounting expert Brittany Brown, Founder and CEO of LedgerGurus.
We’ve also put together this free inventory accounting workflow template which you can download and customize to suit your own business’s tools and processes. You can also watch the webinar below for an overview of the inventory accounting workflow for ecommerce.
Table of Contents
Why is accurate inventory accounting important?
Let’s start by setting a realistic expectation: perfect inventory accounting is nearly impossible.
As Brittany Brown aptly puts it:
“Inventory accounting is like doing laundry. I put two socks in the dryer, but somehow, only one comes out.”
With so many moving parts, there are countless reasons inventory might go missing or become unaccounted for. (Learn more about this in the ‘Common reasons for inventory adjustments’ section below.)
That said, striving for accuracy in inventory accounting is crucial. Why?
Inventory directly affects your business’s value. Whether you’re seeking investment, applying for a loan, or planning to sell your business, potential lenders, investors, or buyers will closely scrutinize your Balance Sheet and Profit and Loss statements. Accurate inventory figures are essential to instill confidence in these numbers.
While perfection isn’t achievable, this guide aims to outline the key steps in inventory accounting to help you establish a process that gets as close to perfect as possible.
If you need help with your inventory accounting, the LedgerGurus team – or any of the accounting and bookkeeping experts in the A2X Directory – can provide you with the support you need!
Operational details that impact your inventory accounting process
Inventory accounting isn’t a “one-size-fits-all” process, especially for ecommerce brands with diverse products and sales channels.
Key factors that will influence how you approach inventory accounting include:
Manufacturing – Do you produce your own products, outsource production, engage in arbitrage, or use a mix of these methods?
Warehousing – Are you using your own warehouse, a 3PL (third-party logistics provider), or a combination (e.g., staging in-house and fulfilling through FBA)?
Sales channels – Do you sell on Amazon, Shopify, eBay, Etsy, Walmart, or a mix of platforms?
These elements directly impact how inventory costs are tracked, allocated, and reconciled. Aligning your accounting process with your production methods, storage logistics, and sales platforms ensures accurate financial reporting, streamlined operations, and better decision-making.
Note – If you work with an accountant or bookkeeper, make sure you communicate these details to them!
Steps: Inventory accounting for ecommerce
Inventory accounting steps for most ecommerce brands will include:
- Forecasting – Predicting future inventory needs based on historical data, trends, and sales projections to ensure optimal stock levels.
- Purchasing – Ordering inventory from suppliers or manufacturers to meet anticipated demand.
- Receiving – Recording and verifying incoming inventory against purchase orders to ensure accuracy and completeness.
- Selling – Recording and tracking inventory reductions as products are sold across your sales channel(s).
- Fulfillment – Picking, packing, and shipping products to customers while updating inventory records to reflect changes.
- Returns – The management of returned inventory, including inspecting, restocking, or discarding items, and reconciling adjustments in inventory records.
- Warehouse counting / true up – Conducting physical inventory counts and reconciling discrepancies with accounting records to ensure accuracy.
Let’s dive into what’s involved with each step, and provide a few extra details about how each step impacts accounting.
1. Forecasting
Inventory accounting begins with forecasting – i.e., predicting your inventory needs for the year/months ahead.
Forecasting your inventory needs will help you maintain optimal stock levels, minimize overstock or stockouts, and align inventory purchases with expected sales – all of which can help you improve financial accuracy and operational efficiency.
Complete the following steps for accurate forecasting.
Step | Details | Accounting impact |
Analyze sales data and trends | Examine historical sales data and identify patterns or trends to help forecast future demand. |
|
Forecast demand | Once you’ve completed your sales analysis, you can predict the quantity of products needed based on sales trends, seasonality, and market factors. | |
Determine lead times | Understand the time it takes to receive inventory after placing an order. | Lead times will ultimately influence when purchases are recorded and how inventory is classified on Balance Sheets (e.g., in transit vs. available). |
Determine quantity and timing of purchases | Calculate the optimal order quantities and scheduling purchases at the right times to ensure sufficient stock (while minimizing holding costs and waste). | Quantity and timing decisions affect cash flow, supplier payments, and the timing of inventory costs in accounting records. |
2. Purchasing
Purchasing involves ordering inventory from suppliers or manufacturers to meet anticipated demand (as forecasted in the previous step).
Purchasing is an important step to consider in inventory accounting because it determines the cost and timing of inventory acquisition, which directly impacts the valuation of inventory on the Balance Sheet and the Cost of Goods Sold (COGS) on the Income Statement.
Accurate purchasing records ensure proper tracking of expenses, alignment with demand, and effective cash flow management.
If you’re self-manufacturing your product, you’ll need to do the following.
Step | Details | Accounting impact |
Determine raw materials and produce a bill of materials | A bill of materials (BOM) is a detailed list of all the raw materials, components, parts, and quantities required to manufacture a finished product. It serves as a comprehensive blueprint for production, outlining everything needed for assembly or manufacturing. | By detailing the materials consumed in manufacturing, the BOM helps allocate costs to finished goods, supports accurate valuation of inventory, and ensures compliance with accounting standards for COGS and financial reporting. |
Come up with a plan for production and produce a production schedule | A production schedule is a detailed plan that outlines what products need to be manufactured, in what quantities, and by when. It aligns production timelines with inventory levels and demand forecasts, ensuring raw materials are available and efficiently used. | This schedule dictates when costs for materials, labor, and overhead are incurred and transferred into work-in-progress or finished goods inventory. |
Order raw materials | Order raw materials as per your BOM and production schedule. | When materials are purchased, they are recorded as inventory assets on the Balance Sheet. Once these materials are used in production, their costs are allocated to work-in-progress or finished goods inventory, eventually contributing to the COGS on the Income Statement. |
If you’re outsourcing your manufacturing, or sourcing and reselling products (product arbitrage), you’ll need to do the following.
Step | Details | Accounting impact |
Determine supplier pricing and come up with an approval process | This step involves negotiating pricing with suppliers and establishing approval workflows to ensure purchases align with budgets and policies. | Clear pricing agreements and approval processes ensure accurate cost tracking and prevent unauthorized or unrecorded purchases, aiding in expense management and financial reporting. |
Issue purchase order | A purchase order (PO) is a formal request sent to a supplier detailing the goods, quantities, and agreed-upon pricing. | Issuing POs creates a financial obligation and provides a reference point for matching invoices and inventory received, ensuring accuracy in accounts payable and inventory records. |
Receive bill | The supplier's invoice is reviewed against the PO and shipment details to verify charges before processing payment. | Receiving and validating bills ensures accurate expense recording and prevents discrepancies between received goods and supplier charges. |
Issue pre-payment to supplier | A pre-payment is made to secure an order, often for custom or high-value inventory purchases. | Pre-payments are recorded as prepaid expenses or advances in accounting, impacting cash flow and requiring adjustments once the goods are received. |
Track shipments | Monitoring the status of orders ensures timely receipt of inventory and helps address delays or discrepancies. | Tracking shipments ensures inventory in transit is accounted for appropriately, maintaining accurate inventory levels and preventing mismatches in financial records. |
3. Receiving
Receiving refers to the process of inspecting, verifying, and recording inventory when it arrives from a supplier.
Receiving impacts inventory accounting by transitioning purchased items into recorded inventory assets on the Balance Sheet.
If you’re self-manufacturing, steps involved with receiving include:
Step | Details | Accounting impact |
Receive raw materials | Record the delivery of materials from suppliers to ensure they match the purchase order and meet quality standards. | Increases raw material inventory on the Balance Sheet. |
Manufacturing the product (according to the bill of materials and production schedule) | Assemble or create the product using raw materials, guided by the bill of materials and production schedule. | Costs of raw materials, labor, and overhead are transferred from raw materials inventory to work-in-progress or finished goods inventory, impacting inventory valuation and COGS calculations. |
Move finished product to finished goods in product tracking | Once production is complete, the finished products are moved from work-in-progress to the finished goods inventory for storage or sale. | This step finalizes the cost allocation, transferring the total production costs to finished goods inventory, which will later be recognized as COGS when the products are sold. |
If you’re outsourcing your manufacturing (or engaging in product arbitrage), steps involved with receiving include:
Step | Details | Accounting impact |
Receive goods | Goods are delivered from the supplier or manufacturer and logged into the system upon arrival. | This step increases inventory assets on the Balance Sheet, initiating the tracking of inventory costs for future sales or usage. |
Inspect quality and quantity and produce a receiving slip | The delivered goods are inspected to ensure they meet the purchase order (PO) specifications, and a receiving slip is created to document the inspection. | Accurate inspection and documentation prevent discrepancies, ensuring inventory valuation reflects only usable and correct items. |
Mark PO as received | The purchase order is updated to indicate that the goods have been delivered and accepted. | Marking the PO as received triggers inventory updates and ensures that accounts payable aligns with received goods. |
Receive final bill | The supplier provides a final invoice for the goods, which is reviewed for accuracy against the purchase order and receiving slip. | The bill establishes the financial liability in accounts payable and ensures accurate expense recording. |
Resolve disputes or pricing differences | Any discrepancies between the PO, receiving slip, or bill are addressed with the supplier to ensure accurate pricing and quality. | Resolving disputes avoids overpayment and ensures inventory costs are accurately reflected in financial records. |
3-way verification of PO, rec slip, bill | This step involves cross-checking the purchase order, receiving slip, and invoice to confirm consistency before payment. | Ensures inventory, accounts payable, and expenses are accurately recorded, preventing financial discrepancies or errors. |
Approval process – pay bill | The bill is approved for payment after all verifications are complete, and the supplier is paid. | Payment reduces accounts payable and impacts cash flow, while ensuring accurate financial records for inventory costs. |
4. Selling
You’ve forecasted, purchased, and received your inventory – now it’s time to sell it!
Selling brings in revenue, but it’s important to remember that it also reduces inventory levels, and inventory systems must be updated to reflect the removal of sold items.
Selling impacts inventory accounting by reducing inventory assets on the Balance Sheet and recording the COGS on the Income Statement. This step ensures accurate financial reporting by matching inventory costs to revenue and provides insight into profitability and stock turnover rates.
Accounting steps for selling inventory include the following.
Step | Details | Accounting impact |
Create sales receipt / invoice AR | A sales receipt or invoice is generated to document the transaction, detailing items sold, quantities, and payment terms for the customer. | This step records revenue in the accounting system and, if unpaid, increases accounts receivable, ensuring accurate tracking of sales income and outstanding customer payments. |
Create picking slip | A picking slip is created to guide warehouse staff in locating and preparing the sold items for shipment. | While this step doesn’t directly impact accounting, it initiates the inventory adjustment process, ensuring inventory records align with physical stock. |
Sales activity reported, recorded, and reconciled | Sales transactions are reported in the accounting system, reconciled with inventory systems, and matched with payments to ensure accuracy. | This step ensures revenue, accounts receivable, and inventory levels are updated accurately, maintaining reliable financial records and preventing discrepancies. Pro tip: A2X can make this process incredibly easy if you’re selling on Amazon, Shopify, Etsy, eBay, or Walmart! |
Calculate COGS | The Cost of Goods Sold (COGS) is calculated based on the costs associated with the inventory sold during the transaction. | COGS is recorded on the Income Statement, reducing inventory on the Balance Sheet and directly impacting profit calculations and gross margin analysis. |
5. Fulfillment
Fulfillment in inventory refers to the process of picking, packing, and shipping products to customers after a sale.
Fulfillment is important for accounting as it updates inventory records to reflect the transfer of goods to customers, reducing inventory assets on the Balance Sheet. It also directly impacts the calculation of COGS, ensuring accurate revenue and expense matching on financial statements.
Proper fulfillment tracking also helps prevent discrepancies between physical stock and accounting records.
If you’re outsourcing fulfillment, then your 3PL will fully handle fulfillment and updates.
If you’re fulfilling orders yourself, follow the steps below.
Step | Details | Accounting impact |
Pick & pack (create a packing slip) | This involves selecting items from inventory to fulfill an order and creating a packing slip to include with the shipment (to help ensure accuracy). | Picking reduces the physical inventory count, while packing creates documentation that supports inventory adjustments, ensuring records reflect the stock used for fulfillment. |
Create a shipping label | A shipping label includes customer details and delivery information for the chosen carrier to ensure the package reaches its destination. | Shipping costs may be recorded as expenses or passed to the customer as revenue, impacting profitability and requiring accurate tracking of associated fees. |
Use the shipping label to ship box | The labeled package is handed over to the shipping carrier for delivery to the customer. | Shipping confirms the fulfillment process and triggers recognition of revenue and the recording of COGS in accounting systems. |
Update fulfillment status | The order status is marked as fulfilled in inventory and sales systems, reflecting that the product has been shipped. | This step ensures inventory records are updated to reduce stock levels, aligning inventory accounting with the actual sale and shipment. It also closes the sales transaction for proper financial reporting. |
6. Returns
Returns in inventory refer to the process of customers sending back products, which may involve inspecting, restocking, or disposing of the returned items.
Returns occur for a variety of reasons (defects, dissatisfaction, etc.), and involve updating inventory and financial records accordingly.
Returns impact inventory accounting by requiring adjustments to inventory levels and reversing COGS for the returned items. They also affect revenue recognition, as refunds or credits may be issued, and necessitate proper tracking to maintain accurate financial reporting and assess the impact on profitability.
Note: To avoid the cost and complexity of managing returned inventory, some brands will introduce a policy that allows dissatisfied customers to keep a product and get refunded (instead of returning the item). Work with an accountant to understand the cost of returns to your business if you’re considering putting a policy like this in place.
To manage returns in inventory accounting:
Step | Details | Accounting impact |
Customer processes return; create a return authorization | The customer initiates the return process, and a return authorization (RA) is issued to approve and track the return. | The RA ensures that the return is logged for tracking purposes, creating a record that will reverse revenue and adjust inventory or COGS once the product is returned. |
Product received back into warehouse or 3PL | The returned product is inspected upon receipt to determine if it can be restocked, needs repair, or should be written off. | Inventory levels are updated, potentially increasing stock for restocked items or recording losses for damaged goods. Accurate adjustments are essential for maintaining correct inventory valuation. |
Inventory value / COGS adjusted | The value of the returned product is recorded, and the COGS is reversed or adjusted to account for the returned inventory. | Adjusting inventory value and reversing COGS ensures accurate financial reporting, aligning sales and inventory records with actual returns and their financial impact. |
7. Warehouse counting / true up
Warehouse counting, also known as a “true up”, involves conducting physical inventory counts to verify the actual stock levels against recorded quantities in inventory systems. It is used to identify and reconcile discrepancies caused by shrinkage, miscounts, or system errors.
Warehouse counting is crucial for accounting because it ensures that inventory records accurately reflect the value of stock reported on the Balance Sheet. Adjustments made during the true up process help correct inventory valuation, align COGS, and provide accurate data for financial reporting, tax compliance, and decision-making.
Warehouse counting steps include:
Step | Details | Accounting impact |
Products counted | Physical inventory is manually counted or scanned to determine the actual quantity of products in stock, identifying discrepancies with recorded inventory levels. | Counting provides the basis for identifying shrinkage, overstock, or miscounted items, highlighting the need for adjustments to maintain accurate inventory valuation in financial records. |
Inventory adjusted | Inventory records are updated to align with the actual stock levels identified during the count, correcting for any discrepancies. | Adjustments affect the inventory value reported on the Balance Sheet and may impact COGS on the Income Statement. These updates ensure accurate financial reporting and help prevent future errors in inventory management. |
Common reasons for inventory adjustments in ecommerce (and the 10% rule)
At the very beginning of this guide, we set the expectation that perfect inventory accounting is nearly impossible. The reality is that you’ll almost always have to make adjustments at the end of an accounting period.
Some common reasons for large adjustments include:
- Expenses that were already included in COGS
- Returns written off that are still available for sales
- Products bought on terms
- Changed order numbers after invoices
- Lost/destroyed in warehouse
- Transit – items in transit
- Phone/email orders
- Amazon reimbursements
- Recognition of landed costs across multiple zones
- Giveaways/marketing
- Undisclosed supplier credits
- Theft
- Timing differences
But… how large of an adjustment is acceptable? Here’s Brittany Brown’s rule of thumb:
“Inventory true ups are a valuable measure of operational effectiveness. If you find yourself adjusting inventory by more than 10% over the course of a year, it’s a red flag that poor processes are leading to significant losses. This indicates it’s time to review and tighten your procedures.
Adjustments will almost always be required with a true up. It’s just part of the inventory life. A good rule of thumb is that adjustments of 10% or less over the course of a year are generally acceptable. Don’t stress over a small discrepancy. Socks get lost in the dryer. Tupperware containers lose their lids. Inventory disappears and even shows back up. However, if you suspect a specific issue, such as theft, take the time to investigate.
Remember, inventory accounting isn’t a journey of perfection – it’s about continuously improving your processes over time.”
We hope that this guide can help you improve processes by outlining the key steps for successful inventory accounting for ecommerce!
Inventory accounting resources
Inventory accounting is a journey. Here are some resources that can help:
- Inventory Accounting Workflow for Ecommerce [Free Template] – Download and make it your own!
- Building a Best Practice Inventory Accounting Workflow for Ecommerce – Watch Brittany Brown explain how to build an inventory accounting process by identifying ownership, dependencies, friction, and technology.
- 3 Inventory Accounting Mistakes (and How to Avoid Them) – Watch our session with Finale Inventory which covers common inventory accounting mistakes for ecommerce.
- A2X Ecommerce Accountant Directory – Find an inventory accounting expert who can help your business.